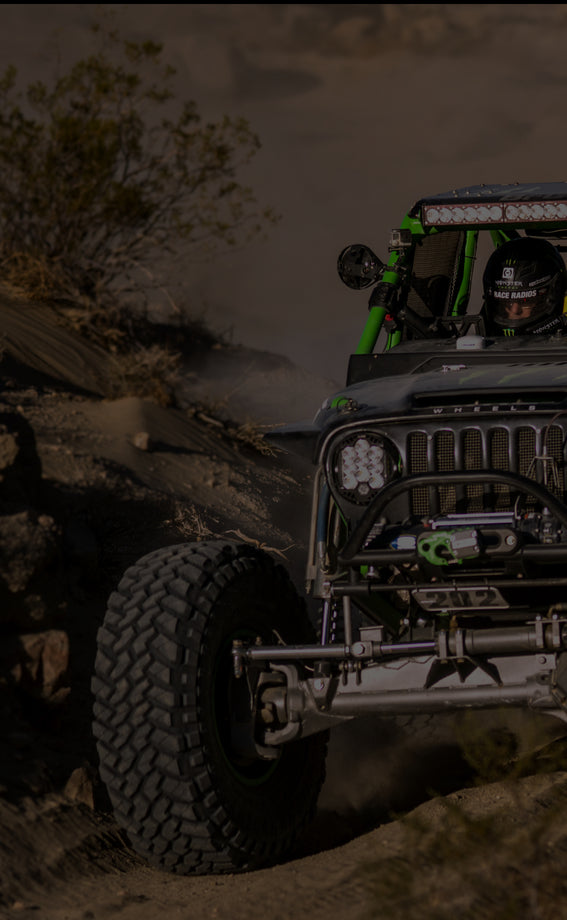
Select Your Vehicle Type
Select Your Vehicle Specifications
We do not have those parts for your vehicle. Please select another part category.
Select Your Vehicle Specifications
It is possible we may not have parts for certain vehicles.
We do not have those parts for your vehicle. Please select another part category.
Where is your Vehicle Registered?
Where is your Vehicle Registered?
WHAT EMISSIONS STANDARD IS YOUR VEHICLE EQUIPPED WITH?
You can find out by inspecting the emissions sticker that is located in your engine compartment.
Vehicle Details
Select the option that best describes your vehicle. We want to make sure the part fits your specific vehicle so we need a little more information from you.
What is your EFN # ?
You can identify your vehicle’s EFN by checking your emission tag located under the hood, on the suspension tower or on the radiator shroud.
SELECT A TOPIC
Order Inquiries
To start your order, please click here. Once you input your vehicle year, make, model, sub-model and type of product you’re looking for, you’ll be shown all the different part numbers that fit. After adding an item to your cart, click the shopping cart icon in the top right of the page to begin our easy checkout process.
If the part is in stock and the order is placed before 11am PT / 2pm ET, the order will ship same day. If the order is placed after those times, the order will be shipped out next business day. If the part is out of stock, it will ship out once back in stock and you will be notified via email.
MagnaFlow ships orders Monday thru Friday, excluding any major holidays. Depending on your state, zip code and the type of shipping method you chose, the expected shipping time will vary. Please see our transit map for more accurate time frames.
Yes, we take all major credit and debit cards.
You can check the status of your order anytime on the following page or by clicking “Track an Order” at the bottom of the page. You will need your order # to continue. If you’re unsure of your order #, please contact us here and include your name, phone number, part number ordered and shipping address, and one of our dedicated Customer Service representatives will get back to you.
By law, you are not permitted to equip your vehicle with federal catalytic converters while residing in California, New York, as well as for some vehicles being registered in Maine.
To ensure you’re picking the correct part, once you enter your vehicle info and click “Next”, you’ll be prompted to select the state in which your vehicle is registered in. Based on your selection, you will be shown only parts compliant with state laws.
If you have any additional questions, please see our Local Emission Standards page.
If you purchased your MagnaFlow part from magnaflow.com, please read below. If you purchased your part from an authorized MagnaFlow reseller, please contact them to receive your order confirmation.
Please contact us here with your name, phone number, part number ordered and your shipping address. We will respond with your order details and send you an order confirmation.
If you purchased your MagnaFlow part from magnaflow.com, please read below. If you purchased your part from an authorized MagnaFlow reseller, please contact them to inquire about your order.
Please contact us here with your name, phone number, part number ordered and your shipping address. We will review the email immediately and respond with your order status.
If you purchased your MagnaFlow part from magnaflow.com, please read below. If you purchased your part from an authorized MagnaFlow reseller, please contact them to initiate your return.
Please contact us here with your name, phone number, part number ordered and your shipping address. Please take pictures of the damaged part(s) as we will need them to further investigate the claim. Depending on the severity of the damage, we will either replace the entire part or send out a replacement component. If you’re missing a component, please identify the component you’re missing and we’ll send you a replacement. Regardless, our dedicated Customer Service team will make sure you’re taken care of.
It’s possible that you can cancel the order if it has not yet shipped. If the order has shipped, you will not be able to cancel and will need to initiate a return here, if you choose to return it.
To check if your order has shipped, please click here. If it hasn’t shipped, please contact us here with your name, phone number, part number ordered and shipping address.
You can also contact us here for any additional inquiries regarding canceling or changing your order.
If the order has not yet shipped, we will process the refund within 3 business days in which you’ll need to contact your credit card company to determine the amount of time they normally take to credit your account. You will receive an email confirmation of the cancelation once processed on our side.
If the order was shipped, you will need to initiate a return here. Once the refund has been processed, approved and received at MagnaFlow’s return facility, we will inspect and process the refund within 5 business days.
Shipping & Returns
You can check the status of your order anytime on the following page or by clicking “Track an Order” at the bottom of the page. You will need your order # to continue. If you’re unsure of your order #, please contact us here and include your name, phone number, part number ordered and shipping address, and one of our customer service representatives will get back to you.
At this time, we are only shipping to the US, Canada and Mexico. If you live in another country and looking to purchase a MagnaFlow part, please contact a local reseller. If you cannot find one, please contact us and we'd be happy to put you in touch with one.
For any orders shipped outside the US, you are responsible for paying any applicable duties and taxes. MagnaFlow is not responsible for covering these charges and will ship the product in accordance with the shipper’s international policies.
We cannot ship MagnaFlow parts to a PO address. We require a physical address. If you do not have a physical address, you can look at having the part shipped to a courier or dedicated pickup center.
We cannot ship MagnaFlow parts to a FPO/APO address. We require a physical address. If you do not have a physical address, you can look at having the part shipped to a courier or dedicated pickup center.
For your protection, orders over $500 require a signature upon delivery.
For any purchases made on MagnaFlow.com, MagnaFlow offers a 30 day return policy for all products that are unused and in the original packaging, effective from the confirmed arrival date of your order. For any products that are used and/or not in original packaging, within or outside of the 30 day timeframe, they will be handled on a case-by-case basis and you may be subject to a restocking fee of up to 20%. For additional information, please see our Returns Policy here.
For any purchases made outside of MagnaFlow.com, please see the reseller’s specific return policy for details. MagnaFlow will not be able to accept returns not purchased on MagnaFlow.com.
If you purchased your MagnaFlow product from magnaflow.com, you can initiate you return by clicking here. You will need your order # and email address associated with the order. Once this information is provided, please follow the instructions indicated on the page, as well as on the return instructions email you receive.
If you do not have your order information, please contact us here. Please include your name, phone number, part number ordered and shipping address. One of our dedicated Customer Service representatives will respond with your order information so you can process the return.
For any purchases made outside of MagnaFlow.com, please see the reseller’s specific return policy for details. MagnaFlow will not be able to accept returns not purchased on MagnaFlow.com.
If you purchased your MagnaFlow product from MagnaFlow.com, when you initiate your return here and the return is approved, you will receive a prepaid shipping label to use. Please follow the instructions in the email and on the shipping labels, as well as carefully package the item. Any items returned to MagnaFlow facilities without using the MagnaFlow provided shipping label will be rejected.
The cost of your shipment will be deducted from your return amount unless the item was covered under warranty, in which MagnaFlow will absorb the return cost.
For any purchases made outside of MagnaFlow.com, please see the reseller’s specific return policy for details. MagnaFlow will not be able to accept returns not purchased on MagnaFlow.com.
If you purchased your MagnaFlow product from MagnaFlow.com, MagnaFlow will cover the cost of return shipping for all warranty returns. For all other returns, MagnaFlow will provide you a prepaid return shipping label using our dedicated carrier discounts. Once the return is received and inspected, we will refund your purchase price less the prepaid shipping amount.
Any items returned without using the MagnaFlow provided shipping label will be rejected.
MagnaFlow will not cover expedited shipping costs over and above the prepaid label provided.
For any purchases made outside of MagnaFlow.com, please see the reseller’s specific return policy for details. MagnaFlow will not be able to accept returns not purchased on MagnaFlow.com.
Technical Inquiries
You can start your search here where you’ll provide your vehicle information, including year, make, model and sub-model. If you have further questions, please contact our technical department here.
EFN stands for “Engine Family Number”. It is found on the emissions control tag underneath the hood of your vehicle. This number is needed to ensure the correct part is provided for your California compliant vehicle. It is illegal to equip a registered California or New York vehicle with a federal and/or non-California compliant part. For more information, please visit the following page.
Standard grade products are manufactured with the required precious metals to be compliant with a properly tuned and operating vehicle.
HM and OEM grade products are designed to function with the Engine Family Number specific designs calling for more precious metals to be used. HM and OEM grades ensure both tailpipe and engine management system compliance is adhered to, while keeping the “check engine light” off. In addition, the extra loading of precious metals will allow for proper engine management interaction and provide additional emissions conversion for vehicles which may not be running at 100%.
Both options will perform equally. Direct-fit parts are easier to install as they are designed to be bolt-on with zero welding required. Universal parts will require professional installation that may include cutting and welding in order to fit. To check the available parts for your vehicle, please start your search here. If you have additional questions, you can contact us here.
Depending on vehicle and weather conditions, internal components may break loose or become defective. If this happens, please initiate a return here and choose “Warranty” as the return reason. We will process the return and ship you free of charge either a brand new part or replacement component (depending on the severity of the damage). Please include any details during your return process as to why you believe the part to be defective, including the sound you’re hearing. This will help us process the warranty exchange quicker.
If you’re having issues with your purchased product fitting your vehicle, please contact us here and one of our dedicated Customer Service representatives will contact you. Please include your name, phone number, part number ordered, shipping address, vehicle information (year, make, model and sub-model) and any details as to why it’s not fitting.
Please see our warranty policy for full details.
No, it will not. It is illegal for a dealer, installer or manufacturer to deny you the OE warranty because you’ve changed the exhaust system. Please refer to the Magnuson Moss Warranty Act of 1975, 15 USC, 2302 and Clean Air Act 42 of USA code 7541 for more information.
All of our exhaust systems use premium quality components, including 409 stainless steel, with the exception of our Diesel Aluminized product line.
Stainless steel mufflers have a polished stainless steel shell and are made of a 100% stainless construction. Nothing looks better or lasts longer than stainless steel.
Aluminized mufflers have stainless internals and necks, but have an aluminized outer shell. Also, the aluminized steel has only a protective coating that is more susceptible to rust.
By definition, P0420 code reads “bank one Catalyst Efficiency low”. A vehicle displaying this code indicates that something is causing the converter to operate out of specification. Further diagnostics and/or inspection is required before determining the part is defective.
General Questions
Please contact us here and include your name and mailing address in the message.
Yes, MagnaFlow does offer sponsorships for select vehicles and events. If you are interested in a sponsorship opportunity, please complete the appropriate application form found here. A member from MagnaFlow’s marketing team will review and be in touch.
MagnaFlow is always searching for vehicles to test-fit new performance exhaust systems and/or direct-fit catalytic converters. If you would like to register your vehicle in our Developer Program, please contact us here.
Members of the press with media-related inquiries may contact the MagnaFlow Marketing team via media@magnaflow.com or 949-858-5900. All communication will be responded to within 1 to 2 business days. For company Information and to learn about MagnaFlow, please visit the About Us page.
For company Information and to learn about MagnaFlow, please visit the About Us page.